In industries such as textiles, where steam is extensively used to power various machines, efficient management of steam condensate is crucial for operational and economic reasons. One of the most effective technologies in this regard is the Condensate Pump — a device engineered to collect and return the unused steam condensate back to the boiler. This not only helps in reusing valuable water but also significantly enhances boiler efficiency and reduces fuel costs.
This article explores the working principle, mechanical and control components, types, and industry standards associated with condensate pumps.
How Does a Condensate Pump Work?
Steam generated from a boiler is used to run industrial machines. Once the steam loses its heat energy during the process, it condenses back into water known as condensate. This condensate typically has 0 TDS (Total Dissolved Solids), making it pure and highly valuable for reuse. However, without a proper management system, this high-quality water often gets wasted.
That’s where the condensate pump comes into action. The unused condensate is channeled into the pump, which then pushes it back to the boiler feed tank. This recirculation process conserves water, reduces fuel consumption (since the condensate is already hot), and increases the lifetime of the boiler due to reduced scaling and impurities.
Mechanical Components of Condensate Pump
The reliability of a condensate pump lies in its robust construction. Below are the primary mechanical components:
- Vessel Tank: The storage chamber for condensate before pumping.
- Header: Typically 1.5x larger than the vessel tank, designed with multiple inlet ports to receive condensate from different lines or machines.
- Water Pipes: Facilitate condensate movement between the machines, the pump, and the boiler.
- Flanges: Ensure tight, secure connections at various joints to avoid leakage.
- Flow Valves: Control and regulate the flow of condensate into and out of the vessel.
- Base Plate: Provides foundational stability and proper mounting for the entire unit.
- Non-Returning Valve (NRV): An essential safety device that prevents backflow, ensuring the condensate doesn’t reverse and cause system malfunction or pressure issues.
Control Systems: Float Control vs. Sensor Control
The functionality of a condensate pump can vary depending on its control mechanism, primarily falling into two categories:
1. Float Control System
This traditional system uses a mechanical float to detect the water level in the vessel. When the level rises, the float triggers a valve, allowing steam pressure to push the condensate toward the boiler. It’s a reliable and cost-effective method, especially for smaller applications.
2. Sensor Control System
A more modern approach, this system uses OMRON sensors, solenoid valves, and indicators. These detect the water level electronically and signal the system to operate accordingly. Sensor-controlled pumps offer greater precision, faster response time, and better integration with automated industrial processes.
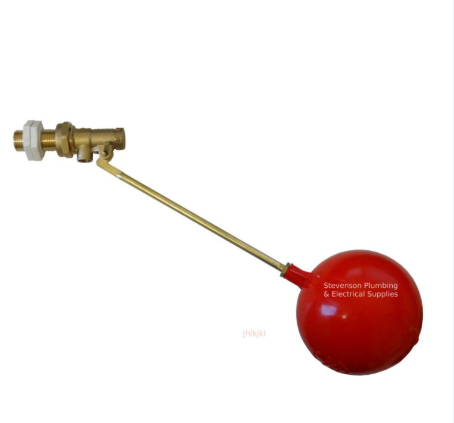
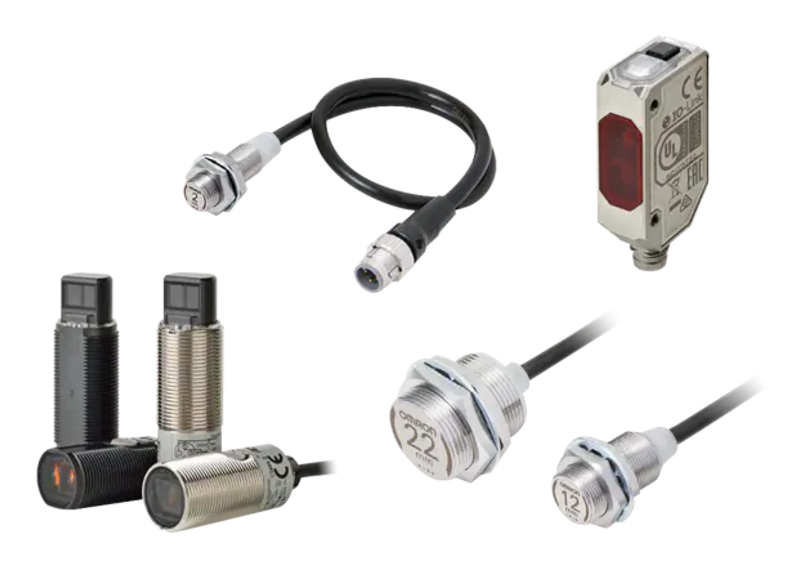
Types of Condensate Pumps (Based on Construction)
There are two main configurations:
🔹 Single Vessel Pumps
- Designed for small-scale operations.
- Ideal when there’s only one boiler or a limited quantity of condensate.
- Comes with a single control system (either float or sensor).
🔹 Multi-Vessel / Double Vessel Pumps
- Used in large industries where multiple boilers are installed.
- Designed to handle large volumes of condensate.
- More economical compared to installing multiple single-vessel pumps.
- Offers better pressure management and operational efficiency.
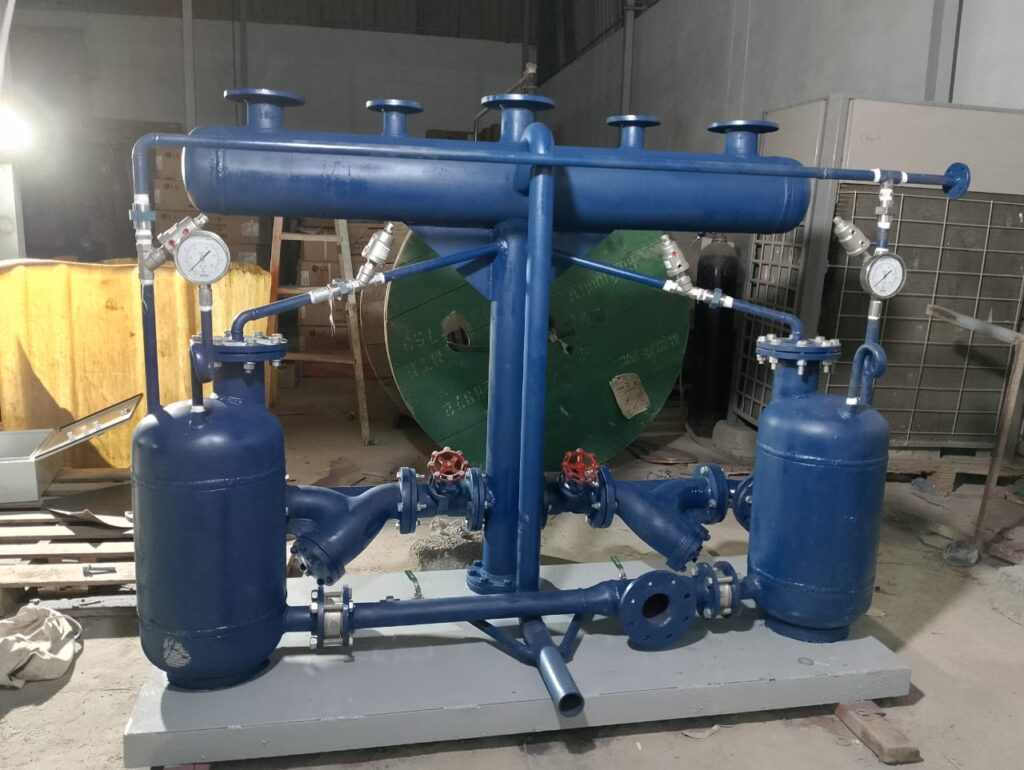
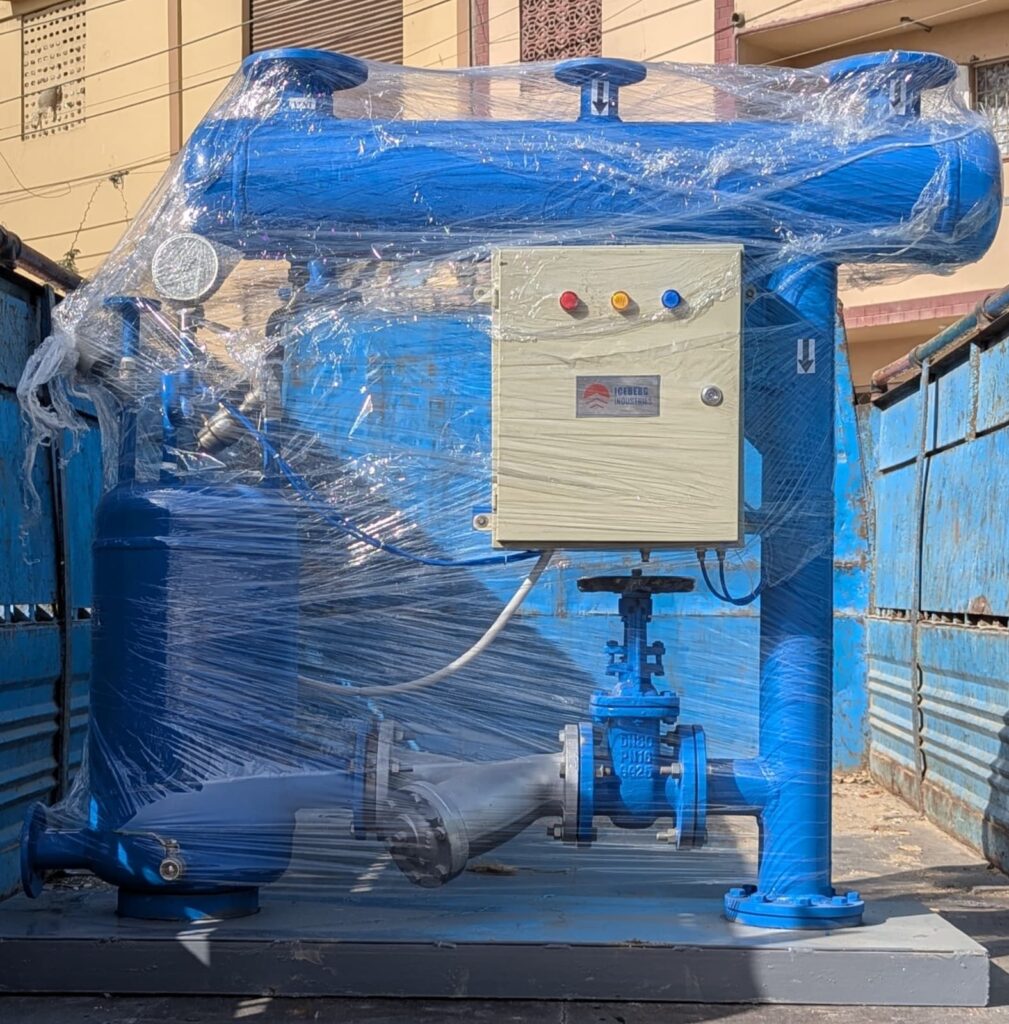
Energy-Free Pumping: Steam-Driven Discharge
One of the most innovative aspects of this system is that no external electrical or mechanical power source is required to move the condensate. Instead, a small amount of steam is used to create pressure, which then pushes the condensate toward the boiler tank — even when the tank is 200–300 feet away. This makes the system highly energy-efficient and cost-effective.
Material Ratings and Technical Specs
- The pump’s piping is constructed with MS Sheet, typically Schedule 40, which supports pressure up to 40 Bars.
- However, under normal operation, condensate pumps usually experience pressures between 10–15 Bars.
- All materials and welding conform to industrial-grade durability standards to ensure safe long-term use.
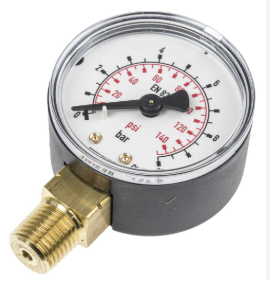
Condensate pumps are not just essential for energy efficiency, but also play a vital role in water conservation, cost reduction, and boiler longevity. Whether you require a compact single-vessel system or a high-capacity multi-vessel unit, our pumps are custom-built to meet your industry’s specific needs.
If you’re planning to install or upgrade your condensate recovery system, feel free to reach out to us for tailored engineering solutions.
Stay connected with us for more in-depth industrial engineering insights.